基本情報
出展製品・サービス
持続可能で積算温度からコンクリートの型枠の取外し強度を計測できるシステム
A sustainable system for measuring concrete formwork removal strength based on accumulated temperature
コンクリートの品質において、打設開始から型枠を取り外すまでの初期養生期間の品質管理が、その将来的な寿命を決定すると言っても過言ではありません。
現代では、セメントと水の化学反応(水和熱)を打設開始時から積分し、その積算温度からコンクリートの強度発現を計測する方法が世界標準となりつつあります。世界中のほぼすべてのシステムでは、センシングデバイスをコンクリート内部に埋め込む形で計測を行っていますが、本システムではセンサーをコンクリート内部に埋め込まず、型枠の外側に設置する方式を採用しています。
この方式により、従来の圧縮試験室に持ち込むことなく、現場で打設から型枠の取り外しまでを連続的にデジタル管理できます。その結果はグラフやカラーマッピングを用いて視覚的に表示され、現場・現場事務所・支店・本社・発注者間でリアルタイムに情報共有できます。さらに、これらのビッグデータの蓄積・保管をも可能にしました。
また、躯体中心部よりも表面側にセンシングデバイスを設置することで、中心部より低い強度が計測され、安全側での判断となります。
そして、このIoTを活用した強度管理システムは、打設から型枠の取外しまでの品質管理を何度も繰返し使用する事を可能にしました。
It is no exaggeration to say that the quality of concrete depends on quality control during the initial curing period, from the start of pouring to the removal of the formwork, as this period plays a crucial role in determining the long-term durability of the concrete.
The method of estimating concrete strength through accumulated temperature, by integrating the heat of hydration - a chemical reaction between cement and water - from the start of pouring, is now becoming the global standard. Almost all existing systems worldwide embed sensing devices inside the concrete. However, this system is different because it places the sensors outside the formwork, allowing continuous digital monitoring from pouring to formwork removal without the need for conventional compression testing. It provides real-time data visualization through graphs and color mapping while also allowing seamless real-time data sharing among key stakeholders, including the construction site, site office, branch office, headquarters, and the client. Additionally, it enables the long-term storage and management of big data for further analysis and optimization.
Furthermore, placing sensing devices on the surface side of the structure rather than at its center results in lower measured strength values compared to the core, providing a more conservative and safety-focused assessment. This IoT-driven strength management system allows for repeated use, ensuring consistent quality control throughout the entire curing process, from pouring to formwork removal.
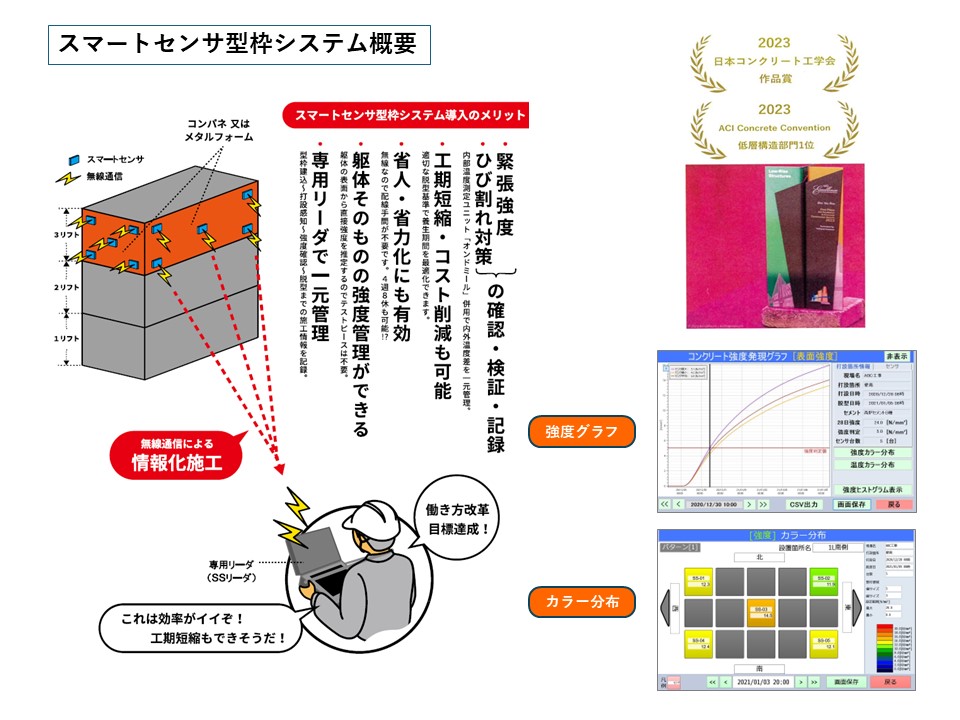
持続可能で積算温度からコンクリートのσ28日(4週)強度を計測できるシステム
A sustainable system for measuring the 28-day (4-week) compressive strength of concrete based on accumulated temperature.
前項1点目の【製品・サービス説明】において、「コンクリートの品質は、打設開始から型枠を取り外すまでの初期養生期間の品質管理が、コンクリートの将来寿命を決めると言っても過言ではありません」と記載しました。しかし、型枠を取り外す時点ではまだ設計基準強度には達しておらず、施工管理者はその後、打設日から28日後(4週強度)の到達強度を確認する義務があります。
従来の28日後の強度確認方法としては、打設時に複数の模擬試験体を作製し、28日後に圧縮試験機で試験を行い、設計基準強度に達しているかどうかを判断していました。しかし、模擬試験体は実構造物と大きさや質量が異なり、水和反応や養生環境にも違いがあるため、現場の実構造物との強度に乖離が生じます。また、圧縮試験後の模擬試験体のコンクリート殻は産業廃棄物となり、最終的な処分が必要になります。
本システムは打設時から型枠の外側に設置され、型枠取り外し時に一旦躯体から離れますが、直後に再度躯体に取り付けられ、28日後(4週強度)まで引き続き情報収集を行います。そして、最終到達強度の計測後に取り外されますが、その後も何度も繰り返し使用できるため、循環型社会に貢献する、環境配慮型の持続可能な強度確認システムと言えます。
In the first point of the previous section, [Product/Service Description], we stated that it is no exaggeration to say that the quality of concrete depends on the quality control during the initial curing period, from the start of pouring until the removal of the formwork. This period plays a critical role in determining the long-term durability of the concrete. However, at the time of formwork removal, the concrete has not yet reached its design standard strength. Therefore, the construction manager is obligated to verify the achieved strength 28 days after the pouring date (4-week strength).
Traditionally, the method for checking the strength after 28 days involved preparing multiple test specimens at the time of pouring and placing them in a compression testing machine after 28 days to determine whether the design standard strength had been met. However, the size and mass of these test specimens differ from actual structures, as do the hydration reactions and curing environments. As a result, the measured strength of the test specimens does not accurately reflect the strength of the actual structure. Furthermore, once the compression tests are completed, the concrete shells of the test specimens must be disposed of as industrial waste.
This system is installed outside the formwork at the time of pouring. When the formwork is removed, it is temporarily detached from the structure but is immediately reattached. It remains in place for 28 days (4-week strength) to continue collecting data.
After measuring the final achieved strength, the system is removed and can be reused multiple times. This makes it an environmentally friendly and sustainable strength verification system that supports a circular economy.
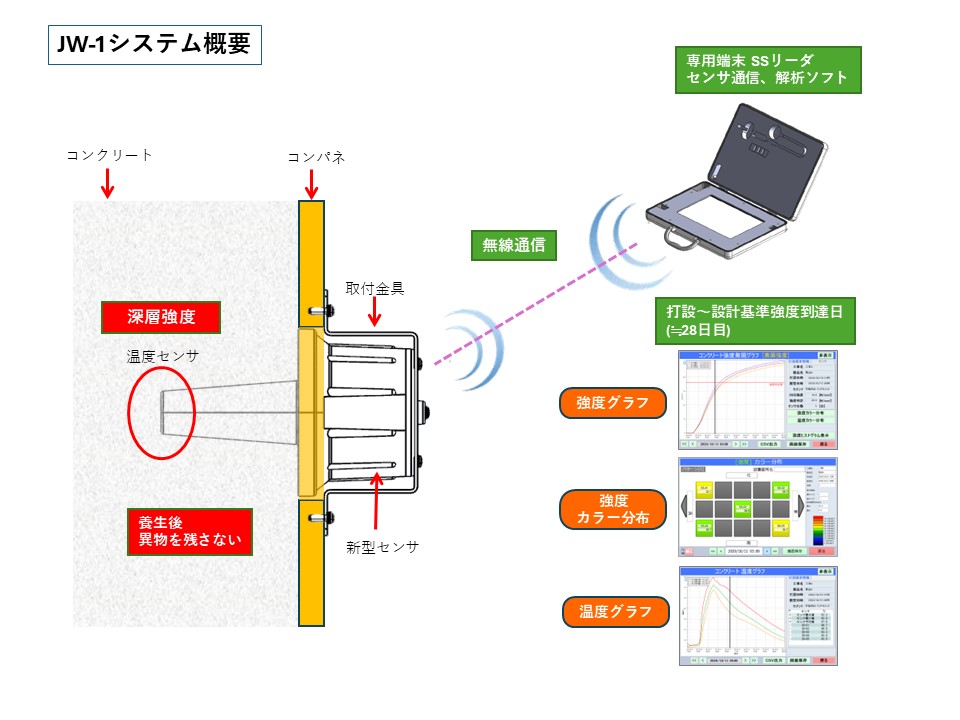
山岳トンネル工法(NATM)の覆工コンクリート打設時に特化した圧力センサーシステム
A pressure sensor system specialized for measuring pressure during lining concrete placement in the New Austrian Tunneling Method (NATM)
山岳トンネル工法(NATM)は、トンネル工法の中で最も普及している工法です。
施工手順としては、掘削→ずり出し→コンクリート吹付け(一次覆工)→ロックボルト打ち込み→覆工コンクリート打設(二次覆工)となりますが、最後の工程である二次覆工がトンネル内部の表面、つまり見え掛かり部分となります。
二次覆工では、トンネル断面の弧を描く超大型の鋼製型枠が用いられます。延長が10mを超える鋼製型枠システム(セントルマシーン)を使用し、一次覆工のコンクリート吹付けとの間にある約30~40cmの空隙に、コンクリートポンプ車を使ってコンクリートを圧送します。
この工程において、ポンプ車の圧送圧力と充填されるコンクリート自重による圧力が相乗効果を生み、セントルマシーンへのダメージは非常に大きくなります。充填速度のタイミングを誤れば、巨大なアーチ型枠の崩壊や人身事故の危険性も高まります。そのため、セントルマシーンに圧力センサーを搭載し、打設の速度と圧力の関係を管理することが広く実施されてきました。
しかしながら、このような重要な役割を担っているにもかかわらず、トンネル工法に特化した圧力センサーは存在せず、長年にわたり土圧計測器が代用されてきました。
本圧力センサーは、トンネル特有のポンプ車による瞬発的な圧力、徐々に加圧される自重圧力、さらにコンクリートに含まれる粗骨材や細骨材の衝突による衝撃緩和などの複合的な圧力を計測可能にした画期的なシステムです。
The New Austrian Tunneling Method (NATM) is the most widely used tunnel construction method.
The construction process follows these steps: excavation, muck removal, spraying of concrete (primary lining), installation of rock bolts, and pouring of lining concrete (secondary lining). The final step, the secondary lining, forms the tunnel’s inner surface, meaning it becomes the exposed part of the structure.
For the secondary lining, extra-large steel formwork that follows the arc of the tunnel cross-section is used. A steel formwork system (centering machine) exceeding 10 meters in length is utilized, and concrete is pumped by a concrete pump truck into the approximately 30cm to 40cm gap between the sprayed concrete (primary lining) and the secondary lining.
At this stage, the pumping pressure from the concrete pump truck and the self-weight of the freshly placed concrete combine to exert a significant load on the centering machine. If the pouring speed is mistimed, it could lead to the collapse of the large arch formwork and increase the risk of serious accidents. Therefore, centering machines are widely equipped with pressure sensors to manage the relationship between pouring speed and pressure.
However, despite their critical role, no pressure sensors specifically designed for tunnel construction exist, and earth pressure gauges have been used as substitutes for many years.
This pressure sensor system is an innovative solution that can measure multiple types of pressure, including instantaneous pressure from concrete pump trucks, gradually increasing self-weight pressure, and impact forces caused by collisions of coarse and fine aggregates within the concrete.
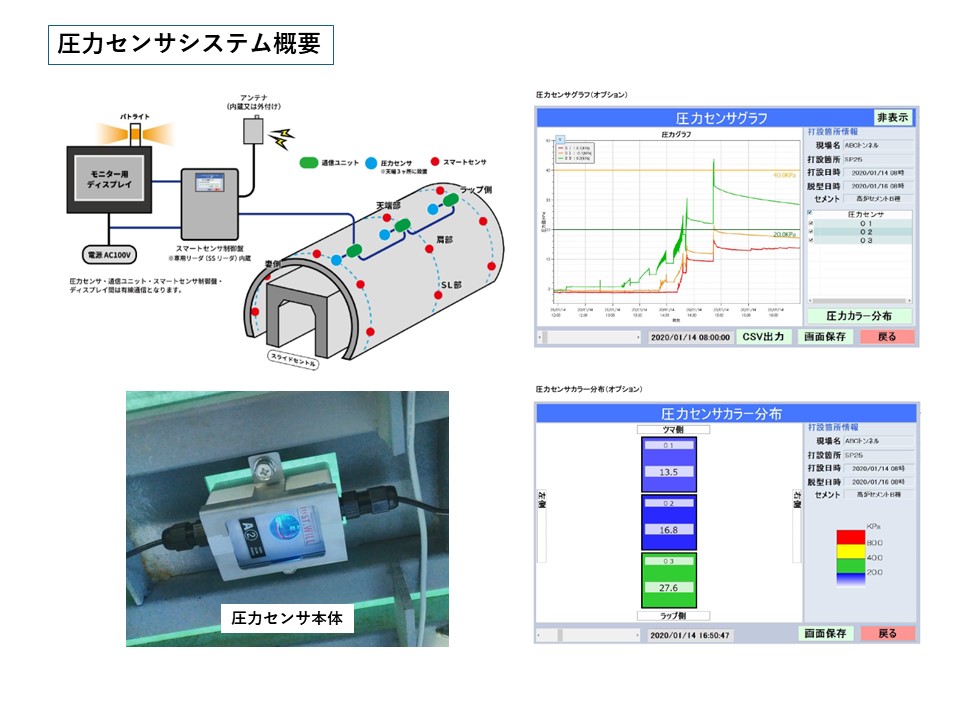